Solar cell production
FEATURES
A leading solar energy manufacturer has partnered with SHL Technologies to develop advanced sub-assembly solutions for a durable copper indium gallium selenide (CIGS) solar cell manufacturing machine. By combining extensive knowledge, experience, and production capabilities, we are able to run complex projects smoothly and efficiently.
- OEM
- Extensive component sourcing experience
- Professional vendor management
- Project management
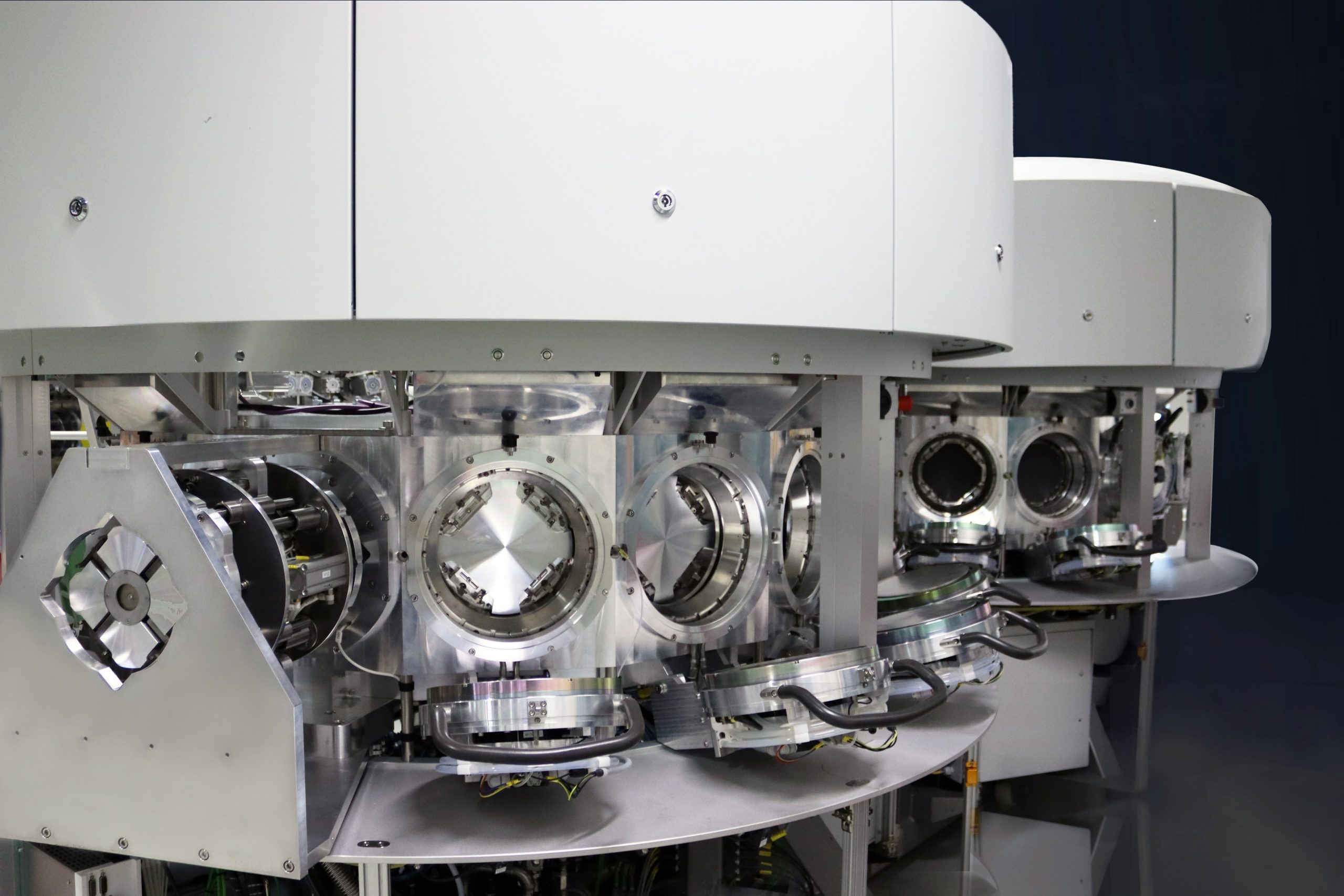
PROJECT SUMMARY
Experienced OEM with a global network
A Swedish company specializing in the production of flexible thin-film solar cells was looking for a development partner with robust industry knowledge and experience in handling complex projects. The company required a partner that not only possessed the key manufacturing capabilities, but one that could also offer cost-effective plans and implement practical project development strategies to ensure a smooth technology transfer.
While there were many candidates with strong manufacturing capabilities, most did not have the necessary experience to guarantee integrated alignment during project transition. On top of having an established system in place, SHL Technologies also demonstrated its proficiency through exceptional in-house experts and vast engineering resources. Putting these factors into consideration, SHL Technologies was eventually chosen as their preferred partner.
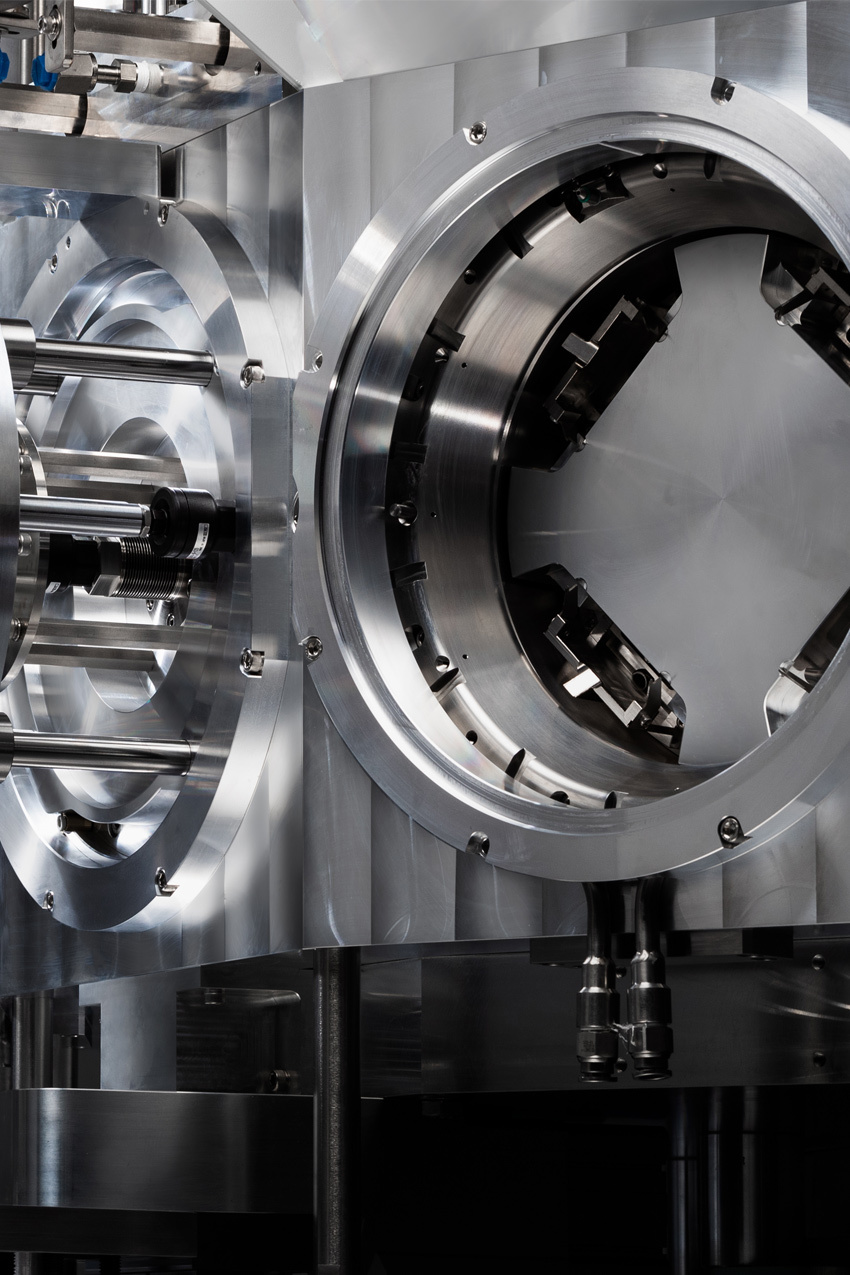
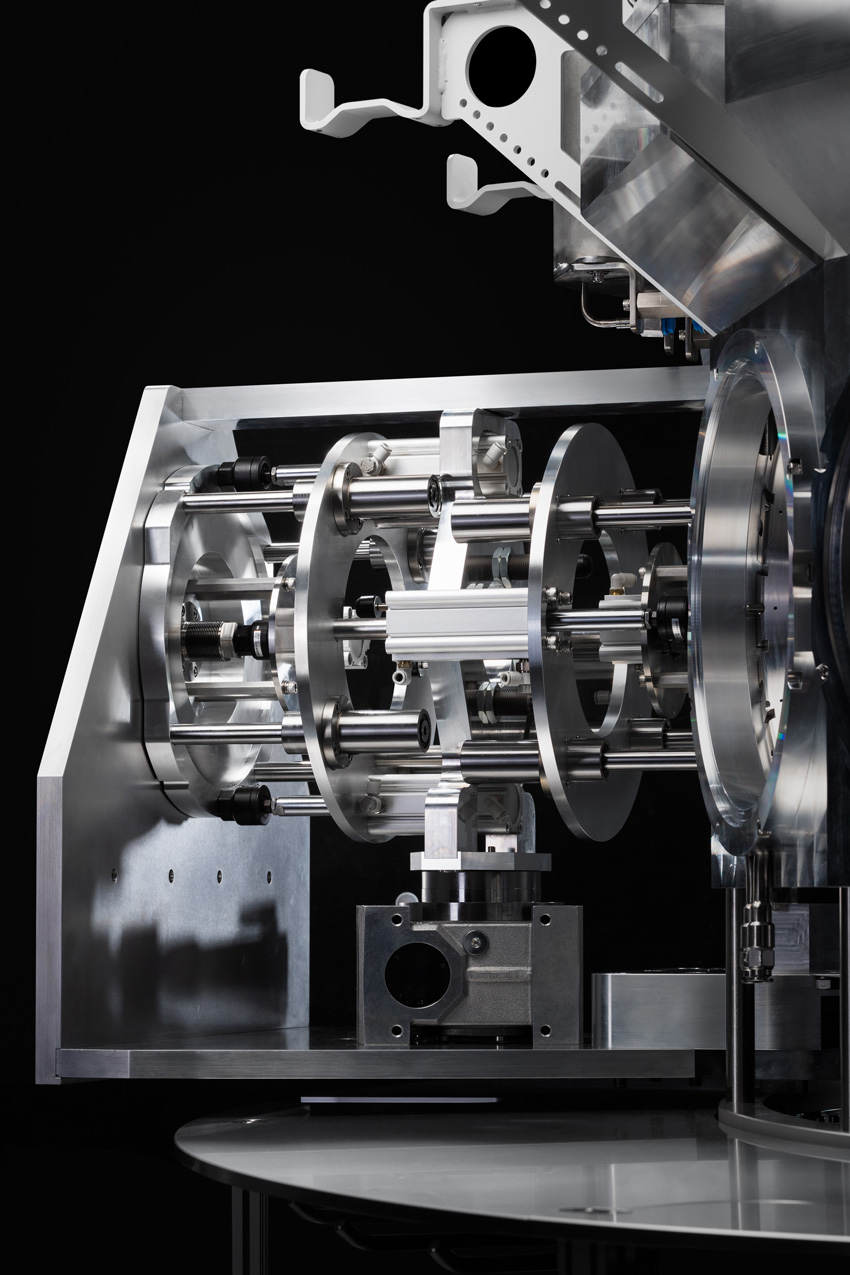
Expanding the partnership
SHL Technologies leveraged its expertise in process engineering as well as in integrated manufacturing to support the production of the next generation solar cell equipment. The project required high tolerance machining capability to ensure accuracy and controlled environment to conduct a pre-cleaning process before assembly took place. SHL Technologies was able to provide these services in-house.
With a solid supply chain network as the backbone, SHL Technologies proposed a more economical and resource-efficient solution to trim the overhead. From handling the procurement of the metal components to providing traceable product development strategies, such as organizing the purchasing orders for effective tracking, SHL Technologies was able to exceed the company’s expectations. Apart from delivering an optimal cost plan, SHL Technologies also increased the level of efficiency in the relevant production steps.
For such an intricate project, having an established communication infrastructure was equally essential. Throughout the development process, in-house experts worked closely with the company to finalize the design and define the testing parameters. Highly competent teams were assigned to address any changes, identify challenges, and devise the appropriate contingency plans. Responsive communications were maintained throughout the processes to assure the fluidity of information exchange.
Multiple visits between engineers further facilitated in-depth discussions where adjustments were made accordingly to avoid any logistical delays. Trainings and documentation of the required modules, such as drawings and working instructions, were all conducted methodically in a timely manner.
The success of the project established SHL Technologies as one of the leading original equipment manufacturers supporting sustainable energy provision. At present, SHL Technologies continues to advance itself as a trusted partner by routinely codifying its techniques and systems to adapt to potential changes. The effort led to the expansion of the partnership where SHL Technologies is expected to further assist in the production and installation of the electrical modules of the equipment.